Destylator przemysłowy to urządzenie, które odgrywa kluczową rolę w procesach separacji substancji chemicznych. Jego działanie opiera się na różnicy temperatur wrzenia składników, co pozwala na ich rozdzielenie. W przemyśle chemicznym i petrochemicznym destylacja jest często wykorzystywana do oczyszczania surowców oraz produkcji wysokiej jakości produktów końcowych. Proces ten polega na podgrzewaniu mieszaniny cieczy, co prowadzi do odparowania składników o niższej temperaturze wrzenia. Następnie para jest schładzana i kondensowana, co pozwala na uzyskanie czystego produktu. W zależności od zastosowania, destylatory mogą mieć różne konstrukcje, takie jak kolumnowe czy prostokątne, a także mogą być wyposażone w dodatkowe elementy, takie jak wymienniki ciepła czy systemy kontroli temperatury. Kluczowym aspektem działania destylatora przemysłowego jest jego efektywność, która zależy od wielu czynników, takich jak ciśnienie atmosferyczne, temperatura oraz skład mieszaniny.
Jakie są zastosowania destylatorów przemysłowych w różnych branżach
Destylatory przemysłowe znajdują szerokie zastosowanie w różnych branżach, co czyni je niezwykle wszechstronnymi urządzeniami. W przemyśle chemicznym służą do produkcji rozmaitych substancji chemicznych, takich jak alkohole, kwasy czy estry. W branży petrochemicznej destylacja jest kluczowym procesem przy produkcji paliw, takich jak benzyna czy olej napędowy. Destylatory są również wykorzystywane w przemyśle spożywczym do produkcji napojów alkoholowych, gdzie proces destylacji pozwala na uzyskanie wysokiej jakości trunków poprzez usunięcie niepożądanych zanieczyszczeń. W farmacji destylatory pomagają w oczyszczaniu substancji czynnych oraz przygotowywaniu roztworów do dalszego wykorzystania. Ponadto, w przemyśle kosmetycznym destylacja jest stosowana do pozyskiwania olejków eterycznych oraz innych składników aktywnych.
Jakie są najważniejsze rodzaje destylatorów przemysłowych
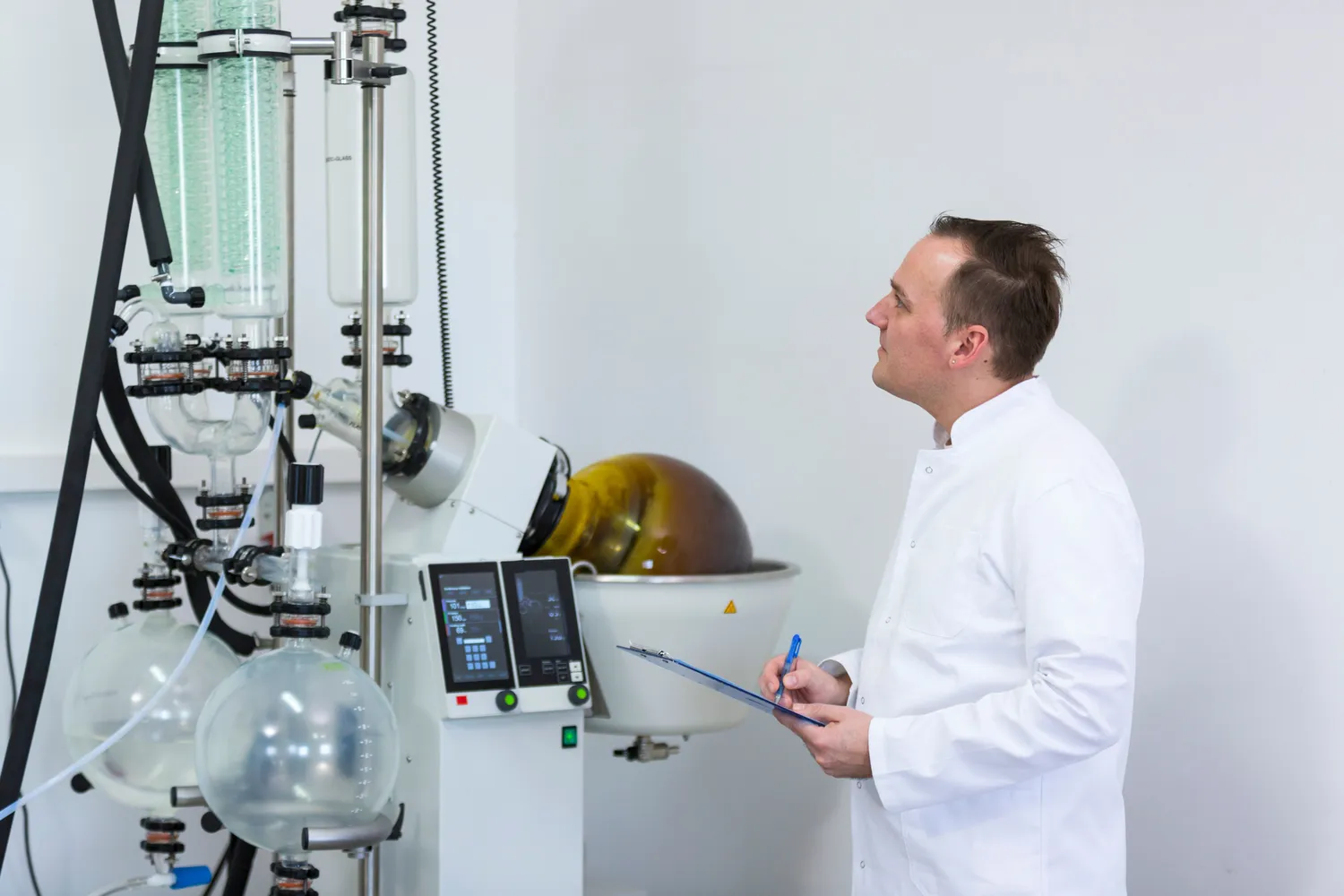
Wśród różnych typów destylatorów przemysłowych wyróżnia się kilka kluczowych rodzajów, które są dostosowane do specyficznych potrzeb produkcyjnych. Destylatory kolumnowe to jedne z najczęściej stosowanych urządzeń w przemyśle chemicznym i petrochemicznym. Charakteryzują się one dużą powierzchnią kontaktu między parą a cieczą, co zwiększa efektywność procesu separacji. Innym popularnym rodzajem są destylatory prostokątne, które są bardziej kompaktowe i łatwiejsze w obsłudze. W przypadku produkcji alkoholi często stosuje się alembiki, które umożliwiają uzyskanie wysokiej jakości trunków poprzez powolną destylację. Istnieją również specjalistyczne destylatory przeznaczone do określonych zastosowań, takie jak destylatory próżniowe, które działają w obniżonym ciśnieniu, co pozwala na destylację substancji o wysokiej temperaturze wrzenia bez ich degradacji.
Jakie są kluczowe zalety użycia destylatorów przemysłowych
Użycie destylatorów przemysłowych niesie ze sobą wiele korzyści, które mają istotny wpływ na efektywność procesów produkcyjnych. Przede wszystkim umożliwiają one uzyskanie wysokiej czystości produktów końcowych poprzez skuteczne usuwanie zanieczyszczeń oraz niepożądanych składników. Dzięki temu można zwiększyć jakość oferowanych wyrobów oraz spełnić rygorystyczne normy branżowe. Kolejną zaletą jest możliwość optymalizacji procesów technologicznych poprzez automatyzację i kontrolę parametrów pracy urządzenia. Nowoczesne destylatory są często wyposażone w zaawansowane systemy monitorowania i regulacji temperatury oraz ciśnienia, co pozwala na precyzyjne dostosowanie warunków pracy do specyfiki danej mieszaniny. Dodatkowo, inwestycja w nowoczesne technologie destylacyjne może prowadzić do znacznych oszczędności energetycznych oraz redukcji kosztów operacyjnych dzięki zwiększonej efektywności procesów separacyjnych.
Jakie są najnowsze technologie w dziedzinie destylacji przemysłowej
W ostatnich latach technologia destylacji przemysłowej uległa znacznemu rozwojowi, co przyczyniło się do poprawy efektywności i jakości procesów separacyjnych. Nowoczesne destylatory są coraz częściej wyposażane w inteligentne systemy zarządzania, które umożliwiają zdalne monitorowanie i kontrolę parametrów pracy. Dzięki zastosowaniu zaawansowanych algorytmów, możliwe jest optymalizowanie procesów w czasie rzeczywistym, co pozwala na szybsze dostosowanie się do zmieniających się warunków produkcji. Wprowadzenie technologii cyfrowych oraz Internetu Rzeczy (IoT) do przemysłu chemicznego otworzyło nowe możliwości w zakresie automatyzacji i integracji różnych procesów produkcyjnych. Ponadto, rozwój materiałów konstrukcyjnych, takich jak kompozyty czy stopy metali o wysokiej odporności na korozję, przyczynił się do zwiększenia trwałości i niezawodności destylatorów. Innowacyjne rozwiązania, takie jak destylacja membranowa czy ekstrakcja cieczy, również zyskują na popularności jako alternatywne metody separacji substancji chemicznych.
Jakie są wyzwania związane z użytkowaniem destylatorów przemysłowych
Mimo licznych zalet, użytkowanie destylatorów przemysłowych wiąże się również z pewnymi wyzwaniami, które mogą wpływać na efektywność ich działania. Jednym z głównych problemów jest konieczność regularnej konserwacji i czyszczenia urządzeń, aby zapewnić ich prawidłowe funkcjonowanie. Osady powstające w wyniku procesów chemicznych mogą prowadzić do obniżenia wydajności oraz jakości produktów końcowych. Dlatego ważne jest wdrożenie odpowiednich procedur konserwacyjnych oraz monitorowania stanu technicznego urządzeń. Kolejnym wyzwaniem jest zarządzanie zużyciem energii, które może być znaczne w przypadku dużych instalacji przemysłowych. W związku z tym wiele firm poszukuje rozwiązań mających na celu optymalizację zużycia energii oraz wykorzystanie odnawialnych źródeł energii w procesach produkcyjnych. Dodatkowo, zmieniające się przepisy dotyczące ochrony środowiska oraz normy jakościowe stawiają przed producentami coraz większe wymagania, co może wymagać inwestycji w nowe technologie oraz dostosowywania istniejących procesów do nowych regulacji.
Jakie są kluczowe czynniki wpływające na wybór destylatora przemysłowego
Wybór odpowiedniego destylatora przemysłowego to kluczowy krok dla każdej firmy zajmującej się produkcją chemiczną lub petrochemiczną. Istnieje wiele czynników, które należy wziąć pod uwagę podczas podejmowania tej decyzji. Przede wszystkim należy określić specyfikę procesu technologicznego oraz rodzaj substancji, które będą poddawane destylacji. Różne typy destylatorów charakteryzują się różnymi parametrami pracy oraz efektywnością separacji, dlatego ważne jest dobranie urządzenia odpowiedniego do konkretnych potrzeb produkcyjnych. Kolejnym istotnym czynnikiem jest wydajność energetyczna urządzenia oraz koszty eksploatacyjne. Warto zwrócić uwagę na nowoczesne rozwiązania technologiczne, które mogą przyczynić się do obniżenia kosztów operacyjnych oraz zwiększenia efektywności energetycznej. Niezwykle istotna jest również jakość wykonania i materiały użyte do budowy destylatora, które wpływają na jego trwałość i niezawodność.
Jakie są różnice między destylacją a innymi metodami separacji
Destylacja to jedna z wielu metod separacji substancji chemicznych, ale wyróżnia się ona swoimi unikalnymi cechami i zaletami w porównaniu do innych technik. W przeciwieństwie do filtracji czy ekstrakcji, które polegają na fizycznym oddzieleniu składników na podstawie ich właściwości fizycznych lub chemicznych, destylacja opiera się na różnicy temperatur wrzenia substancji. Dzięki temu możliwe jest uzyskanie wysokiej czystości produktów końcowych poprzez selektywne odparowanie i kondensację składników o różnych temperaturach wrzenia. Inną popularną metodą separacji jest chromatografia, która pozwala na rozdzielanie składników na podstawie ich interakcji z fazą stacjonarną i ruchomą. Choć chromatografia może być bardziej precyzyjna w niektórych zastosowaniach, to jednak często wymaga dłuższego czasu analizy oraz bardziej skomplikowanego sprzętu. W przypadku dużych skali produkcji destylacja często okazuje się bardziej opłacalna i wydajna niż inne metody separacji.
Jakie są przyszłe kierunki rozwoju technologii destylacyjnej
Przyszłość technologii destylacyjnej wydaje się obiecująca dzięki ciągłemu postępowi naukowemu oraz innowacjom technologicznym. W miarę jak rośnie zapotrzebowanie na bardziej ekologiczne i efektywne procesy produkcyjne, rozwijają się nowe metody destylacji, takie jak destylacja membranowa czy superkrytyczna ekstrakcja dwutlenkiem węgla. Te nowoczesne techniki mogą oferować lepsze wyniki przy mniejszym zużyciu energii oraz surowców naturalnych. Ponadto rosnąca świadomość ekologiczna społeczeństwa sprawia, że przedsiębiorstwa zaczynają inwestować w technologie minimalizujące negatywny wpływ na środowisko naturalne. W przyszłości możemy również spodziewać się większej integracji systemów automatyki i sztucznej inteligencji w procesach destylacyjnych, co pozwoli na jeszcze dokładniejsze monitorowanie i kontrolę parametrów pracy urządzeń. Rozwój materiałów o wysokiej odporności na korozję oraz innowacyjne rozwiązania konstrukcyjne mogą przyczynić się do zwiększenia trwałości i niezawodności destylatorów przemysłowych.
Jakie są koszty związane z zakupem i eksploatacją destylatora przemysłowego
Koszty związane z zakupem i eksploatacją destylatora przemysłowego mogą być znaczące i powinny być starannie analizowane przed podjęciem decyzji o inwestycji w to urządzenie. Koszt zakupu zależy od wielu czynników, takich jak typ destylatora, jego wydajność oraz dodatkowe funkcje technologiczne. Na przykład nowoczesne kolumnowe destylatory o dużej wydajności mogą być znacznie droższe niż prostsze modele przeznaczone do mniejszych instalacji. Poza kosztami zakupu należy również uwzględnić koszty instalacji oraz uruchomienia urządzenia, które mogą obejmować prace budowlane oraz dostosowanie infrastruktury zakładu produkcyjnego do wymogów nowego sprzętu. Koszty eksploatacyjne obejmują zużycie energii elektrycznej oraz mediów pomocniczych takich jak para wodna czy chłodziwo, a także koszty konserwacji i serwisowania urządzenia. Regularna konserwacja jest kluczowa dla utrzymania wysokiej efektywności pracy destylatora oraz minimalizacji ryzyka awarii.